Самый первый километр: как производят автомобильные шины Ⅰ фото
Выбирая новый комплект шин для своего автомобиля, мы практически всегда задаемся вопросом – а сколько тысяч километров они смогут пройти? Сегодня же мы задумались о другом. Каков условный «первый километр» в жизни автомобильной шины? Точнее, тот «километр», который она проходит, чтобы стать, собственно, готовой автомобильной шиной.
На территории России свои заводы разместило уже немало известных на весь мир шинных брендов. Один из наиболее современных открыла в 2016 году компания Bridgestone. Он расположен в Ульяновске и выпускает около двух сотен различных типоразмеров шин в размерностях от 13 до 19 дюймов – для легковых автомобилей, кроссоверов и внедорожников. Часть продукции отправляется к автопроизводителям для первичной комплектации, а это важное подтверждение высокого доверия к продукции. Специалисты Ульяновского завода Bridgestone и помогли нам подробнее разобраться, какой путь проходит шина, чтобы «стать самой собой».
Сырье – химические компоненты, проволока и ткань для корда, каучук – поступает на завод из многих стран мира по собственным цепочкам поставок производителя. Основные химикаты приходят из Японии и Европы, что-то поставляется из стран Азии, Африки, ну и, собственно, от российских поставщиков. Опасения, что Россию обделяют качеством, абсолютно беспочвенны. Мало того, что все сырье сопровождается сертификатами качества, оно проходит еще и дополнительный контроль в собственной химической лаборатории, по внутренним стандартам Bridgestone (а они еще более строги) на стадии приемки и отправки в работу. Внутренние стандарты бренда едины вне зависимости от того, в какой стране мира расположен завод, ведь продукция идет не только на местный рынок, но и отправляется на экспорт. Производственный процесс имеет очень высокую степень автоматизации, техника просто не допустит, чтобы некачественное сырье попало в производственное оборудование.
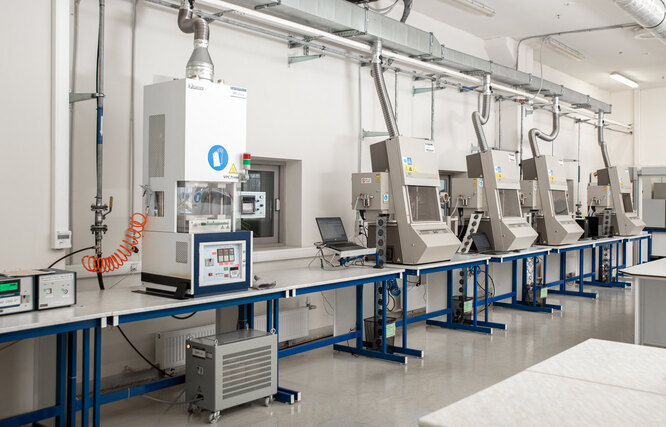
Лаборатория контроля качества материалов
Терминология
Чтобы разобраться в процессе производства шины, нужно обязательно запомнить два слова. Произносятся они достаточно сложно, но без процессов и оборудования, которые скрываются за этими словами на шинном заводе, – никуда.
– Экструдирование (экструзия) – процесс получения изделия путем продавливания вязкого расплава или пасты материала через формующее отверстие. Соответственно, аппарат, который осуществляет эту операцию, называется экструдер.
– Каландрирование – процесс обработки материалов для выравнивания толщины, повышения плотности, гладкости поверхности (или тиснения рисунка). Оборудование для этого процесса называется каландр – это такой барабанный пресс с расположенными один под другим валами, между которыми пропускается материал.
Точкой отсчета начала производства шины можно считать процесс резиносмешивания – именно от этой точки начинается путь к будущей шине. Резиновую смесь специалисты называют компаунд. И этот компаунд может (и должен) быть разным – для разных типов шин. Тем, кто следит за автомобильными гонками, это понятно: для разных температур и покрытий гонщики используют шины разных компаундов. Но и к обычным дорожным шинам применим точно такой же подход. Очевидно, что зимняя шина, рассчитанная на работу в условиях минусовых и околонулевых температур, должна быть мягче, а летняя – жестче.
Смешивание различных компаундов происходит при разных температурах, более того, разные температуры используются и на разных стадиях процесса. На стадии получения так называемой маточной смеси (по-английски этот термин напоминает по звучанию фамилию знаменитого актера – masterbatch) используются температуры в диапазоне от 100 до 160 ℃. Особого температурного режима, к примеру, требуют компаунды с содержанием диоксида кремния (силики), весьма популярного в наше время компонента шинных смесей. На второй, финальной, стадии смесеобразования, где в состав добавляются компоненты, которым предстоит сработать на стадии вулканизации, используются более низкие температуры – около 90–105 ℃. Иначе этот самый процесс вулканизации может активироваться сам по себе. А до него – согласно технологии – пока еще далеко.
Параллельно резиносмешиванию протекают еще два процесса – каландрирование текстильного полотна, которое будет использовано для производства шин, и экструдирование проволоки для металлокорда (ранее на других заводах он тоже каландрировался, но современные технологии позволяют использовать только экструдирование). Нарезка готовых «полуфабрикатов» происходит сразу с учетом того, для какой шины они готовятся. К примеру, для разных шин она происходит под разным углом.
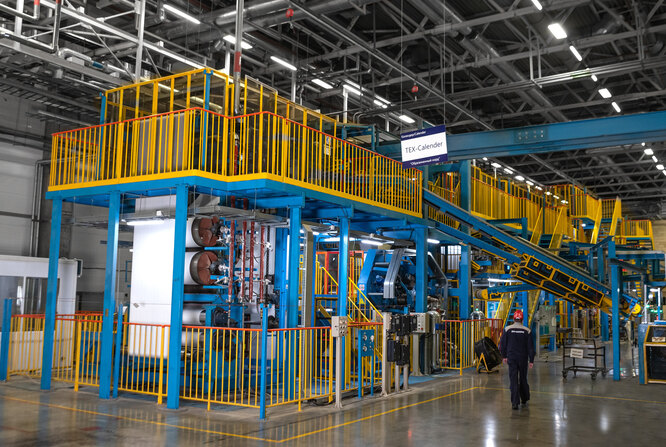
Текстильный каландр – оборудование для обрезинивания текстильного полотна
Active Multicell Compound II
Завод в Ульяновске – единственный из европейских заводов, который работает с новейшей смесью Active Multicell Compound II. Изначально она использовалась только в Японии. Запатентованная резиновая смесь нового поколения используется для изготовления нешипованных (фрикционных) зимних шин и обеспечивает их долговечность, превосходную управляемость и безопасность.
В состав этой смеси входит мелкодисперсный диоксид кремния и нанополимеры, которые способствуют увеличению трения. В результате резина протектора плотно соприкасается с поверхностью льда на дороге, а сила сцепления повышается на большом пятне контакта. Более того, нанотехнологичный полимер в сочетании с силикой делают шину эластичной даже при предельно низких температурах. Еще одна особенность этого компаунда – микропоры, которые позволяют сократить тормозной путь.
Работа с Active Multicell Compound II – предмет особой гордости специалистов российского завода. Шины, для которых эта смесь используется, актуальны и популярны не только на российском рынке, но и в странах Скандинавии, куда на экспорт уходит немалая часть такой продукции.
Технологии постоянно развиваются. К примеру, в условиях борьбы за улучшение экологических качеств автомобилей все актуальнее становится снижение массы шины без ущерба ее прочности и износостойкости. Специалисты Bridgestone разрабатывают все более совершенные резиновые смеси для обрезинивания компонентов шин, испытывают и используют новые армирующие материалы.
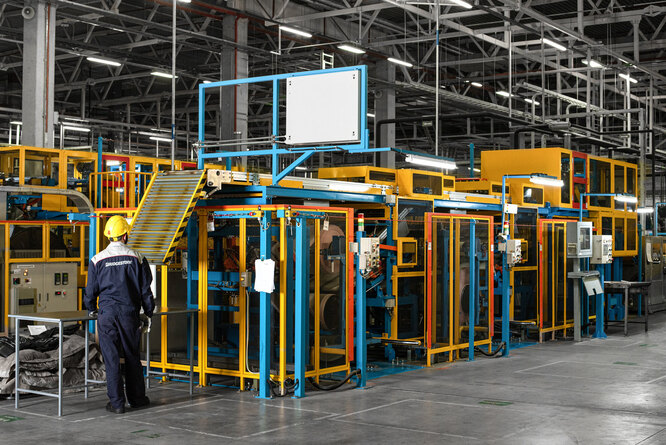
Оборудование для изготовления боковины
Автомобильная шина только внешне выглядит этакой простой монолитной резиновой штуковиной. На самом деле для ее изготовления нужно 10–15 (а порой и более) различных деталей. Да-да, именно деталей. Причем собственно на резиновые смеси приходится… только половина составляющих. В среднем на легковую шину уходит немногим более 6 кг резины (конечно же, это очень усредненный показатель – все зависит от модели и размера). А вот остальные 50% – это текстиль, металл и другие составляющие.
Как мы уже говорили, на заводе параллельно может изготавливаться большое количество (до 30–40 в день) типоразмеров шин. Но большого «промежуточного» запаса здесь стараются не держать – только оперативный запас для непосредственной работы. Зато на этой стадии происходит еще один этап контроля качества – на этот раз уже готовых, но не собранных в единую шину деталей-полуфабрикатов. Каждая линия оборудована большим количеством сенсоров, проверяющих такие параметры, как толщина, вес, позиции наложения компонентов на полуфабрикатах. Степень автоматизации практически полная, человеческий фактор практически исключен. Но оператор иногда все-таки осуществляет дополнительный контроль.
И вот на следующем этапе необходимые детали собираются в одну конструкцию – так называемую сырую шину, с обработанной изнутри специальными антиадгезионными смазками (чтобы не прилипала «ненужной» стороной в вулканизаторе) поверхностью. Сырой она называется потому, что, для того чтобы стать готовой, шине необходимо пройти таинство вулканизации. Но опять же – это будет несколько позже. А пока в дело вступает еще один предмет гордости ульяновских шинников – автоматизированная система доставки и распределения сырых шин. На всем промежутке от сборки до вулканизации рука человека к такой заготовке не прикасается.
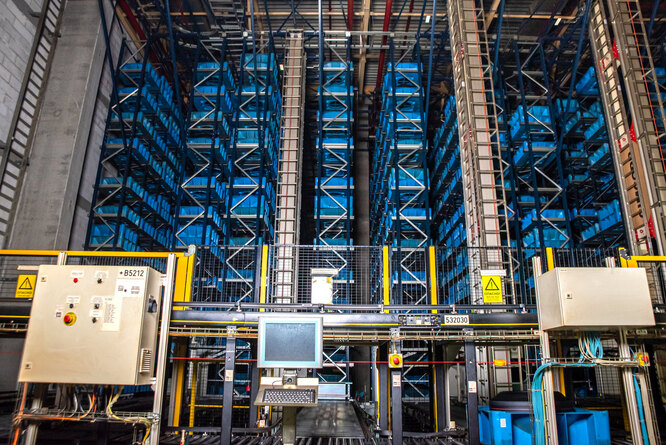
Автоматизированный склад сырых шин
Под потолком завода смонтирована специальная система доставки шин со сборки на промежуточный (буферный) склад, а затем – на вулканизацию. Выглядит немного космически: сверху к шине вдруг протягивается манипулятор от специальной тележки, забирает шину, грузит в эту тележку и увозит. На буферном складе каждой шине автоматически присваивается индивидуальный адрес. Теперь система автоматически отслеживает, когда и от какой вулканизационной установки поступит запрос «мне нужна такая-то заготовка». И снова манипулятор забирает сырую шину, передает другой маленькой тележке под потолком. На каждом отрезке такого пути система несколько раз считывает штрихкоды и проверяет, не сбилась ли шина с верной дороги. Вновь человеческий фактор практически исключен: автоматизация позволяет безошибочно организовать параллельное производство множества типоразмеров.
Итак, тележка подвозит шину к вулканизатору и опускает в специальную корзинку, откуда в нужное время заготовку заберет еще один манипулятор и положит в вулканизатор. Именно здесь шина приобретает свой окончательный вид, а заодно и получает рисунок протектора. За это отвечает специальная пресс-форма – своя для каждой модели и размера.
Жар и лед
Если взглянуть на новенькую, еще не касавшуюся асфальта шину, можно поразиться обилию мелких деталей. Красивый рисунок ламелей, ребрышки-перегородки, тисненые надписи, символы и логотипы, «волоски» литников… Все эти элементы формируются пресс-формами. Но как удается поддерживать чистоту самих пресс-форм? Ведь они находятся в контакте с сырой резиной, которая элементарно липкая. Оказывается, для регулярной очистки пресс-форм используется сухой лед. Причем эффект его использования двойной. Во-первых, частицы льда подаются на пресс-форму под давлением и действуют как своеобразная «пескоструйка», только не повреждающая поверхность, а лишь щадяще очищающая ее. Во-вторых, игра идет на разнице температур и температурных коэффициентов. За счет температурного удара налипающие кусочки резины, нагар отскакивают от поверхности пресс-формы, оставляя ее чистой и готовой к дальнейшему использованию. В результате таких периодических очисток (периоды определяются для каждого случая индивидуально) пресс-форма сохраняет свои качества практически все то время, пока ее рисунок остается актуальным для производства шин.
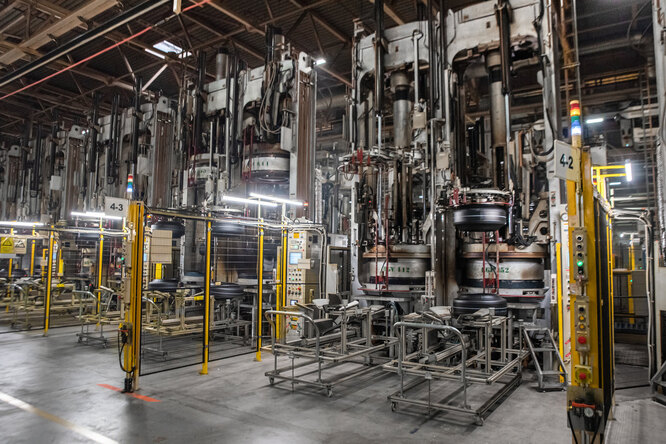
Процесс вулканизации шин
И вот шина «запечена» в вулканизаторе и готова окончательно. Оборудование позволяет достаточно быстро и гибко перенастраивать вулканизаторы на производство разных моделей и размеров. Нормативы времени разнятся в зависимости от участка производства, но в целом никто не заинтересован затягивать процесс. Наоборот, на заводе гордятся гибкостью своего производства, не забывая напоминать, что «гибкость» – это в принципе один из столпов философии Bridgestone.
А готовые шины попадают… думаю, что вы правильно догадались – снова на контроль качества. Абсолютно вся продукция проходит финальную инспекцию. Большая часть этих проверок снова проходит в полностью автоматическом режиме, в том числе автоматический контроль на машинах однородности и баланса. Как терпеливый пациент, шина проходит даже рентген-контроль, где проверяется на наличие металлических включений и иных дефектов распределения компонентов.
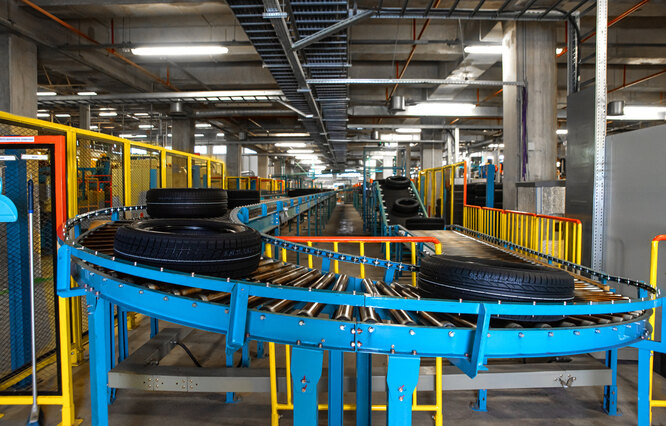
Конвейерная линия участка финальной инспекции
Но есть на этой стадии контроля и участие человека. Причем участие это очень важное, а специалисты, осуществляющие такие проверки, проходят очень длительное обучение и тренинги. Такое участие самых опытных мастеров – традиционная составляющая японского подхода к качеству. Сколь совершенна ни была бы автоматика, но именно за специалистами решающее слово. У них есть определенный процесс – стандартный набор действий, движений, взглядов. Они осматривают каждую шину, и это особый завораживающий процесс, позволяющий уже на финальном этапе найти какой-то ускользнувший дефект.
Но и это еще не всё. Образцы готовой продукции, отбираемые по определенному алгоритму, отправляются в заводскую лабораторию контроля качества. Здесь они проходят дополнительный контроль как неразрушающими (контроль габаритных размеров и проверки площади пятна контакта), так и разрушающими методами. К последним относятся анализ конструкции и распределения компонентов в шине, высокоскоростной тест, тесты на долговечность (износ) и выносливость борта.
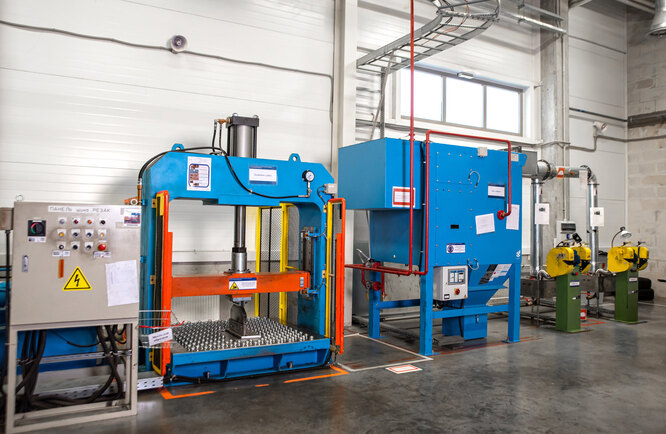
Лаборатория контроля качества готовой продукции
А для нешипованных зимних шин, которые изготавливаются с использованием микропористой смеси (помните, мы отдельно говорили о технологии Active Multicell Compound II?), предусмотрен и еще один тестовый цикл – на проверку пористости резины, определение коэффициента вспенивания.
На горяченькое!
Отдельная история – ошиповка шин. Зачастую производители отдают ее на аутсорс специализированным компаниям. В Bridgestone предпочитают устанавливать шипы своими силами. Для некоторых моделей ошиповка вообще происходит, пока шина буквально еще горячая. Это позволяет достичь сохранности резинового слоя в процессе шиповки, а после остывания шип надежно фиксируется в шине. Современные машины для ошиповки считывают лазером положение каждого отверстия, автоматически вставляют шипы в шину и измеряют уровень выступа шипа (технология машинного зрения), который затем также проверяется вручную на каждой шине.
Любопытно, но говоря о процессе шиповки, нельзя не упомянуть об использовании… обычного мыла. Казалось бы, какую роль оно играет в производстве шин? А вот какую! В определенной дозировке, рассчитываемой автоматически, мыльный раствор позволяет шипу плавно войти в отверстие в шине, сохраняет целостность резинового слоя вокруг шипа, что положительно сказывается на эксплуатационных свойствах ошипованной шины.
Точность и комплексность настроек оборудования позволяют применять шипы направленной конструкции. То есть они устанавливаются строго под определенным углом к направлению качения шины. Такие шипы не только обеспечивают лучшее сцепление, но и менее разрушительны для дорожного покрытия.
Если все в порядке – то партия свеженьких шин отправляется уже на основной склад дожидаться отгрузки.
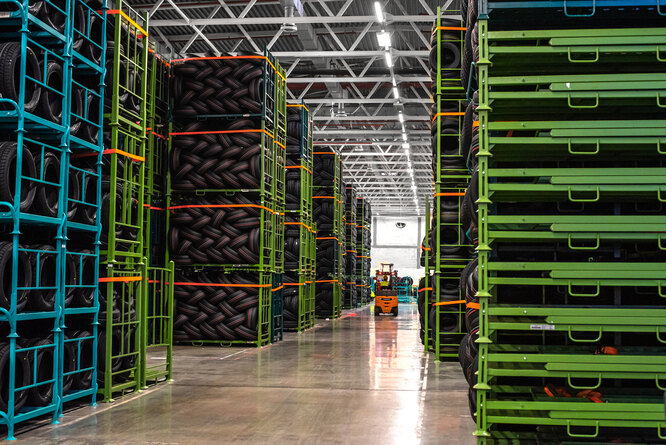
Склад готовой продукции
Адресаты могут быть как российскими, так и зарубежными. Около 20% производимой продукции отправляется на экспорт в страны СНГ, страны Скандинавии, а в ближайшее время этот список пополнится Германией и Польшей.
Но это уже не тот самый «первый километр», а гораздо более дальние маршруты...
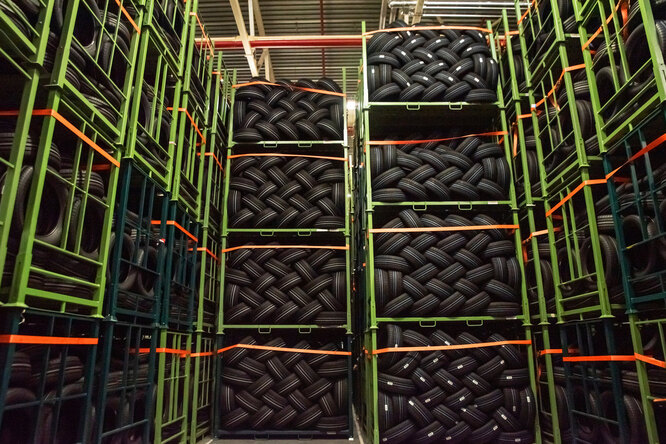
На территории России свои заводы разместило уже немало известных на весь мир шинных брендов. Один из наиболее современных открыла в 2016 году компания Bridgestone. Он расположен в Ульяновске и выпускает около двух сотен различных типоразмеров шин в размерностях от 13 до 19 дюймов – для легковых автомобилей, кроссоверов и внедорожников. Часть продукции отправляется к автопроизводителям для первичной комплектации, а это важное подтверждение высокого доверия к продукции. Специалисты Ульяновского завода Bridgestone и помогли нам подробнее разобраться, какой путь проходит шина, чтобы «стать самой собой».
Сырье – химические компоненты, проволока и ткань для корда, каучук – поступает на завод из многих стран мира по собственным цепочкам поставок производителя. Основные химикаты приходят из Японии и Европы, что-то поставляется из стран Азии, Африки, ну и, собственно, от российских поставщиков. Опасения, что Россию обделяют качеством, абсолютно беспочвенны. Мало того, что все сырье сопровождается сертификатами качества, оно проходит еще и дополнительный контроль в собственной химической лаборатории, по внутренним стандартам Bridgestone (а они еще более строги) на стадии приемки и отправки в работу. Внутренние стандарты бренда едины вне зависимости от того, в какой стране мира расположен завод, ведь продукция идет не только на местный рынок, но и отправляется на экспорт. Производственный процесс имеет очень высокую степень автоматизации, техника просто не допустит, чтобы некачественное сырье попало в производственное оборудование.
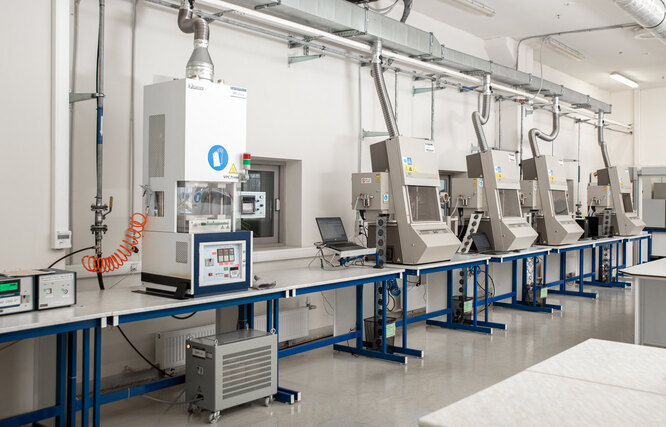
Лаборатория контроля качества материалов
Терминология
Чтобы разобраться в процессе производства шины, нужно обязательно запомнить два слова. Произносятся они достаточно сложно, но без процессов и оборудования, которые скрываются за этими словами на шинном заводе, – никуда.
– Экструдирование (экструзия) – процесс получения изделия путем продавливания вязкого расплава или пасты материала через формующее отверстие. Соответственно, аппарат, который осуществляет эту операцию, называется экструдер.
– Каландрирование – процесс обработки материалов для выравнивания толщины, повышения плотности, гладкости поверхности (или тиснения рисунка). Оборудование для этого процесса называется каландр – это такой барабанный пресс с расположенными один под другим валами, между которыми пропускается материал.
Точкой отсчета начала производства шины можно считать процесс резиносмешивания – именно от этой точки начинается путь к будущей шине. Резиновую смесь специалисты называют компаунд. И этот компаунд может (и должен) быть разным – для разных типов шин. Тем, кто следит за автомобильными гонками, это понятно: для разных температур и покрытий гонщики используют шины разных компаундов. Но и к обычным дорожным шинам применим точно такой же подход. Очевидно, что зимняя шина, рассчитанная на работу в условиях минусовых и околонулевых температур, должна быть мягче, а летняя – жестче.
Смешивание различных компаундов происходит при разных температурах, более того, разные температуры используются и на разных стадиях процесса. На стадии получения так называемой маточной смеси (по-английски этот термин напоминает по звучанию фамилию знаменитого актера – masterbatch) используются температуры в диапазоне от 100 до 160 ℃. Особого температурного режима, к примеру, требуют компаунды с содержанием диоксида кремния (силики), весьма популярного в наше время компонента шинных смесей. На второй, финальной, стадии смесеобразования, где в состав добавляются компоненты, которым предстоит сработать на стадии вулканизации, используются более низкие температуры – около 90–105 ℃. Иначе этот самый процесс вулканизации может активироваться сам по себе. А до него – согласно технологии – пока еще далеко.
Параллельно резиносмешиванию протекают еще два процесса – каландрирование текстильного полотна, которое будет использовано для производства шин, и экструдирование проволоки для металлокорда (ранее на других заводах он тоже каландрировался, но современные технологии позволяют использовать только экструдирование). Нарезка готовых «полуфабрикатов» происходит сразу с учетом того, для какой шины они готовятся. К примеру, для разных шин она происходит под разным углом.
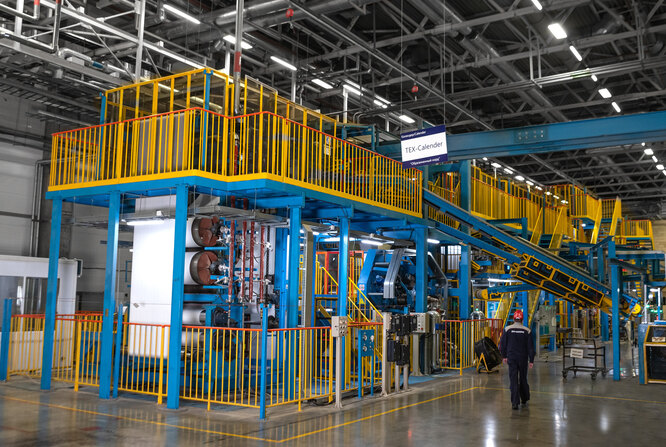
Текстильный каландр – оборудование для обрезинивания текстильного полотна
Active Multicell Compound II
Завод в Ульяновске – единственный из европейских заводов, который работает с новейшей смесью Active Multicell Compound II. Изначально она использовалась только в Японии. Запатентованная резиновая смесь нового поколения используется для изготовления нешипованных (фрикционных) зимних шин и обеспечивает их долговечность, превосходную управляемость и безопасность.
В состав этой смеси входит мелкодисперсный диоксид кремния и нанополимеры, которые способствуют увеличению трения. В результате резина протектора плотно соприкасается с поверхностью льда на дороге, а сила сцепления повышается на большом пятне контакта. Более того, нанотехнологичный полимер в сочетании с силикой делают шину эластичной даже при предельно низких температурах. Еще одна особенность этого компаунда – микропоры, которые позволяют сократить тормозной путь.
Работа с Active Multicell Compound II – предмет особой гордости специалистов российского завода. Шины, для которых эта смесь используется, актуальны и популярны не только на российском рынке, но и в странах Скандинавии, куда на экспорт уходит немалая часть такой продукции.
Технологии постоянно развиваются. К примеру, в условиях борьбы за улучшение экологических качеств автомобилей все актуальнее становится снижение массы шины без ущерба ее прочности и износостойкости. Специалисты Bridgestone разрабатывают все более совершенные резиновые смеси для обрезинивания компонентов шин, испытывают и используют новые армирующие материалы.
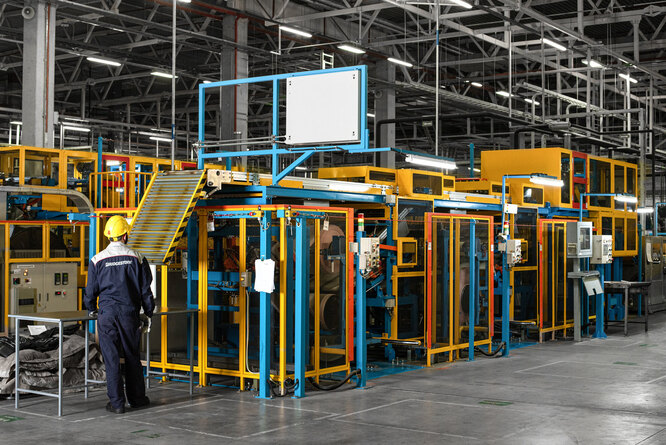
Оборудование для изготовления боковины
Автомобильная шина только внешне выглядит этакой простой монолитной резиновой штуковиной. На самом деле для ее изготовления нужно 10–15 (а порой и более) различных деталей. Да-да, именно деталей. Причем собственно на резиновые смеси приходится… только половина составляющих. В среднем на легковую шину уходит немногим более 6 кг резины (конечно же, это очень усредненный показатель – все зависит от модели и размера). А вот остальные 50% – это текстиль, металл и другие составляющие.
Как мы уже говорили, на заводе параллельно может изготавливаться большое количество (до 30–40 в день) типоразмеров шин. Но большого «промежуточного» запаса здесь стараются не держать – только оперативный запас для непосредственной работы. Зато на этой стадии происходит еще один этап контроля качества – на этот раз уже готовых, но не собранных в единую шину деталей-полуфабрикатов. Каждая линия оборудована большим количеством сенсоров, проверяющих такие параметры, как толщина, вес, позиции наложения компонентов на полуфабрикатах. Степень автоматизации практически полная, человеческий фактор практически исключен. Но оператор иногда все-таки осуществляет дополнительный контроль.
И вот на следующем этапе необходимые детали собираются в одну конструкцию – так называемую сырую шину, с обработанной изнутри специальными антиадгезионными смазками (чтобы не прилипала «ненужной» стороной в вулканизаторе) поверхностью. Сырой она называется потому, что, для того чтобы стать готовой, шине необходимо пройти таинство вулканизации. Но опять же – это будет несколько позже. А пока в дело вступает еще один предмет гордости ульяновских шинников – автоматизированная система доставки и распределения сырых шин. На всем промежутке от сборки до вулканизации рука человека к такой заготовке не прикасается.
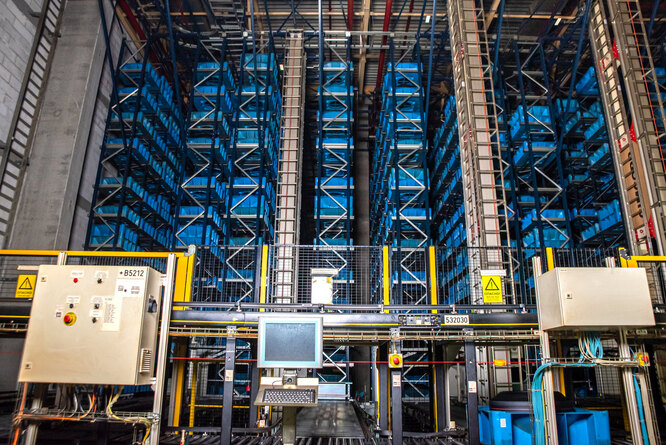
Автоматизированный склад сырых шин
Под потолком завода смонтирована специальная система доставки шин со сборки на промежуточный (буферный) склад, а затем – на вулканизацию. Выглядит немного космически: сверху к шине вдруг протягивается манипулятор от специальной тележки, забирает шину, грузит в эту тележку и увозит. На буферном складе каждой шине автоматически присваивается индивидуальный адрес. Теперь система автоматически отслеживает, когда и от какой вулканизационной установки поступит запрос «мне нужна такая-то заготовка». И снова манипулятор забирает сырую шину, передает другой маленькой тележке под потолком. На каждом отрезке такого пути система несколько раз считывает штрихкоды и проверяет, не сбилась ли шина с верной дороги. Вновь человеческий фактор практически исключен: автоматизация позволяет безошибочно организовать параллельное производство множества типоразмеров.
Итак, тележка подвозит шину к вулканизатору и опускает в специальную корзинку, откуда в нужное время заготовку заберет еще один манипулятор и положит в вулканизатор. Именно здесь шина приобретает свой окончательный вид, а заодно и получает рисунок протектора. За это отвечает специальная пресс-форма – своя для каждой модели и размера.
Жар и лед
Если взглянуть на новенькую, еще не касавшуюся асфальта шину, можно поразиться обилию мелких деталей. Красивый рисунок ламелей, ребрышки-перегородки, тисненые надписи, символы и логотипы, «волоски» литников… Все эти элементы формируются пресс-формами. Но как удается поддерживать чистоту самих пресс-форм? Ведь они находятся в контакте с сырой резиной, которая элементарно липкая. Оказывается, для регулярной очистки пресс-форм используется сухой лед. Причем эффект его использования двойной. Во-первых, частицы льда подаются на пресс-форму под давлением и действуют как своеобразная «пескоструйка», только не повреждающая поверхность, а лишь щадяще очищающая ее. Во-вторых, игра идет на разнице температур и температурных коэффициентов. За счет температурного удара налипающие кусочки резины, нагар отскакивают от поверхности пресс-формы, оставляя ее чистой и готовой к дальнейшему использованию. В результате таких периодических очисток (периоды определяются для каждого случая индивидуально) пресс-форма сохраняет свои качества практически все то время, пока ее рисунок остается актуальным для производства шин.
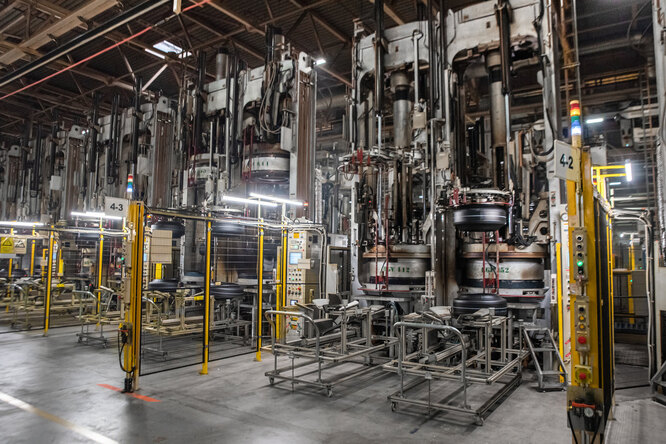
Процесс вулканизации шин
И вот шина «запечена» в вулканизаторе и готова окончательно. Оборудование позволяет достаточно быстро и гибко перенастраивать вулканизаторы на производство разных моделей и размеров. Нормативы времени разнятся в зависимости от участка производства, но в целом никто не заинтересован затягивать процесс. Наоборот, на заводе гордятся гибкостью своего производства, не забывая напоминать, что «гибкость» – это в принципе один из столпов философии Bridgestone.
А готовые шины попадают… думаю, что вы правильно догадались – снова на контроль качества. Абсолютно вся продукция проходит финальную инспекцию. Большая часть этих проверок снова проходит в полностью автоматическом режиме, в том числе автоматический контроль на машинах однородности и баланса. Как терпеливый пациент, шина проходит даже рентген-контроль, где проверяется на наличие металлических включений и иных дефектов распределения компонентов.
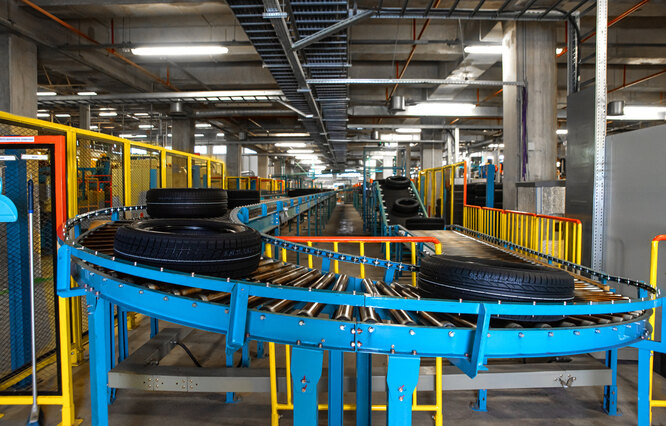
Конвейерная линия участка финальной инспекции
Но есть на этой стадии контроля и участие человека. Причем участие это очень важное, а специалисты, осуществляющие такие проверки, проходят очень длительное обучение и тренинги. Такое участие самых опытных мастеров – традиционная составляющая японского подхода к качеству. Сколь совершенна ни была бы автоматика, но именно за специалистами решающее слово. У них есть определенный процесс – стандартный набор действий, движений, взглядов. Они осматривают каждую шину, и это особый завораживающий процесс, позволяющий уже на финальном этапе найти какой-то ускользнувший дефект.
Но и это еще не всё. Образцы готовой продукции, отбираемые по определенному алгоритму, отправляются в заводскую лабораторию контроля качества. Здесь они проходят дополнительный контроль как неразрушающими (контроль габаритных размеров и проверки площади пятна контакта), так и разрушающими методами. К последним относятся анализ конструкции и распределения компонентов в шине, высокоскоростной тест, тесты на долговечность (износ) и выносливость борта.
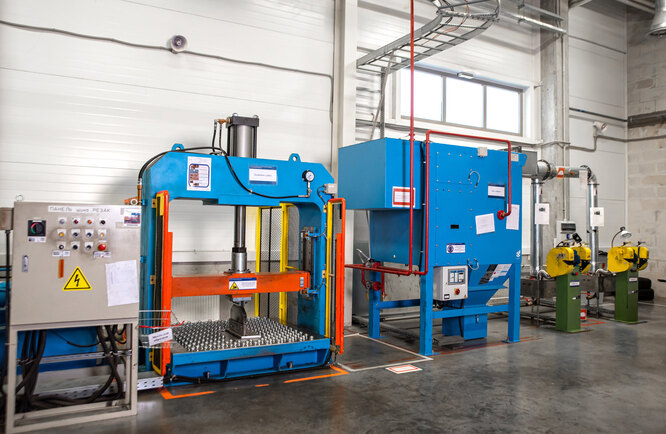
Лаборатория контроля качества готовой продукции
А для нешипованных зимних шин, которые изготавливаются с использованием микропористой смеси (помните, мы отдельно говорили о технологии Active Multicell Compound II?), предусмотрен и еще один тестовый цикл – на проверку пористости резины, определение коэффициента вспенивания.
На горяченькое!
Отдельная история – ошиповка шин. Зачастую производители отдают ее на аутсорс специализированным компаниям. В Bridgestone предпочитают устанавливать шипы своими силами. Для некоторых моделей ошиповка вообще происходит, пока шина буквально еще горячая. Это позволяет достичь сохранности резинового слоя в процессе шиповки, а после остывания шип надежно фиксируется в шине. Современные машины для ошиповки считывают лазером положение каждого отверстия, автоматически вставляют шипы в шину и измеряют уровень выступа шипа (технология машинного зрения), который затем также проверяется вручную на каждой шине.
Любопытно, но говоря о процессе шиповки, нельзя не упомянуть об использовании… обычного мыла. Казалось бы, какую роль оно играет в производстве шин? А вот какую! В определенной дозировке, рассчитываемой автоматически, мыльный раствор позволяет шипу плавно войти в отверстие в шине, сохраняет целостность резинового слоя вокруг шипа, что положительно сказывается на эксплуатационных свойствах ошипованной шины.
Точность и комплексность настроек оборудования позволяют применять шипы направленной конструкции. То есть они устанавливаются строго под определенным углом к направлению качения шины. Такие шипы не только обеспечивают лучшее сцепление, но и менее разрушительны для дорожного покрытия.
Если все в порядке – то партия свеженьких шин отправляется уже на основной склад дожидаться отгрузки.
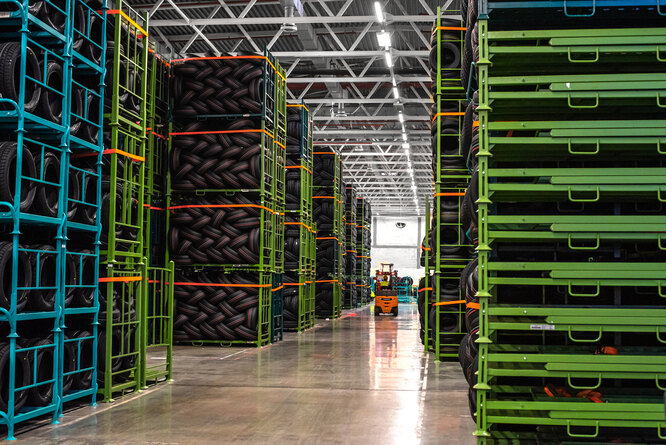
Склад готовой продукции
Адресаты могут быть как российскими, так и зарубежными. Около 20% производимой продукции отправляется на экспорт в страны СНГ, страны Скандинавии, а в ближайшее время этот список пополнится Германией и Польшей.
Но это уже не тот самый «первый километр», а гораздо более дальние маршруты...
+5
151
- Комментарии
Нет комментариев. Ваш будет первым!
Войдите или зарегистрируйтесь чтобы добавлять комментарии